Manufacturing
|
Austral are one of the few companies in the world dedicated solely to the
manufacture of marine propellers. We produce propellers of all types up to 72"
(1.83m) diameter for use on both pleasure and commercial craft.
Austral are marine propeller specialists and as such our plant and equipment is
purpose built with this aim alone. Our facility is totally self contained and
includes a CAD/CAM design centre, pattern shop, modern non ferrous foundry,
machine shop with CNC capability, finishing section and quality control
department. State of the art technology is used extensively throughout the plant
in propeller design, tooling manufacture, production scheduling, electronic
propeller balancing, quality inspection and calibration.
Austral prides itself on its ability to satisfy a total propeller design concept
within a short manufacturing lead-time. We manufacture propellers of superior
styles, to a high quality standard and at a "value for money" price.
Watch
Video - Austral Machining a Stainless Steel Propeller
|
Manufacturing Process
|
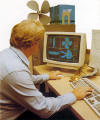
CAD drawing of pattern
|
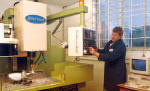
CAM machining of pattern
|
CAD/CAM
Developed
Propeller styles are designed and new patterns are
produced using the latest CAD /CAM computer technology.
|
Pattern
Making
For greater accuracy our propeller castings are made from
"full" metal patterns, not indexed from single blade wooden patterns.
|
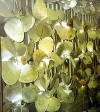 Fixed Patterns
|
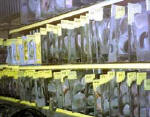 Pattern Plates
|
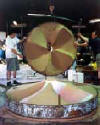 Moulding -
Kaplan Propeller
|
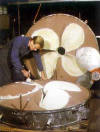 Moulding - Aquafoil
Propeller
|
Moulding
Most propeller moulds are made from a special resin sand
which forms a rigid two part mould ensuring more accurate and sound
castings.
|
Casting Only Premium grade
metals are used in the manufacture of Austral propellers. Each metal batch
is independently certified to conform to alloy specification before delivery
to our premises. |
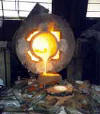 Casting - Large
Propeller
|

Casting - Small Propellers |
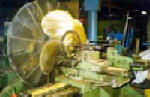 Machining -
Flat Bed Lathe
|
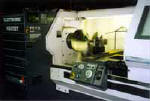 Machining -
Electronic Lathe
|
Machining
A variety of CNC machines and specialised boring, facing
and electronic lathes are used to accurately machine Austral propellers
|
Pitching
Austral uses PropScan® pitch verification measurement
equipment during the manufacturing process to ensure pitch accuracy conforms
to ISO class tolerances at pre-determined radii across the blade face. |
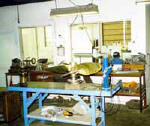 Pitching with
PropScan®
|
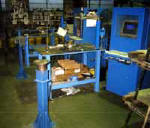 Pitching
Station
|
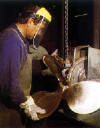 Belt Finishing
|
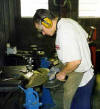 Hand Finishing
|
Finishing
The propeller castings are then ground on various special purpose
abrasive machines |
Balancing
For smoothness, propellers are firstly static balanced
then finally electronically balanced on a computerised balance machine.
Dynamic balancing is also available.
|
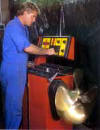 Electronic
Balancing
|
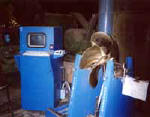 Dynamic Balancing
|
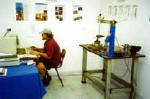 Quality Control
|
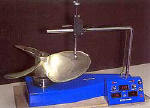 PropScan® Pitch
Verification
|
Quality
Control During manufacture and upon completion,
each propeller is individually checked for accuracy of track, diameter,
pitch, balance, blade form and finish. Manufacturing details of each custom
made propeller are recorded for future reference. |
Shipping Worldwide Austral
propellers are now exported to over 40 countries worldwide. Austral produces
high quality marine propellers at very competitive prices within
particularly short manufacturing lead times. |
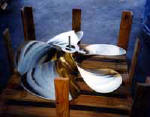 Crating for
Export
|
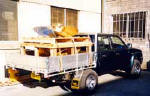 Propellers ready for Airfreight
|
Take a Look
Around Austral Propellers Factory
|
|
CAD/CAM AND CNC
MACHINING
|
The use of the latest technology and advanced CAD/CAM software is an integral
part of Austral's manufacturing procedures . The design can be assessed for
shape and profile then individual sections can be analysed to determine their effectiveness, or otherwise, in
operation.
Once the design has been theoretically proven, the
computer generates machining toolpaths using surfaces
from the propeller drawing. Basically the complete
machining of the propeller can then be simulated on the
computer screen to verify such things as tool selection,
cutter direction, clearances, surface blending etc.
When these machining toolpaths have been verified they are then down loaded to a CNC vertical machining
centre (VMC). By transmitting precise X-Y-Z co-ordinates guides the VMC tool to
machine the propeller pattern exactly as it was originally drawn. Using this
technology, new prototype "test propellers" are produced and water tested within
our ongoing R&D programme.
Once a new design has been proven by exhaustive testing the latest technology can then parametrically produce toolpaths
for any combination of diameter and pitch. Resulting from this extensive R&D
programme some exciting new propeller designs have been produced. This advanced
technology ensures Austral propellers are not only of superior design, but the
finished products are now consistently superior, both in terms of overall
quality and accuracy, to propellers made from traditional manual pattern making
methods.
|
Austral Metals
|
NIBRAL (Nickel Aluminium Bronze)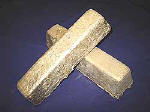
This premium high tensile alloy is recognised, throughout the world, as one of the best metals available for marine
propeller manufacture. The alloy basically has no zinc and with an average tensile strength of 85,000lbs per sq.inch
gives much greater resistance than Manganese Bronze to
bending, flexing and corrosion. Its durability makes it ideal for cupped
propellers, high HP engines and for heavy commercial use.
ALUMINIUM
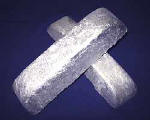
This high strength premium magnesium aluminium has good ductility which means in most cases, upon impact the propeller
will bend rather than break. The alloy is saltwater resistant and unlike die castings Austral propellers can easily be altered
in pitch or cupped. It is used to produce our saildrive, outboard and sterndrive propellers.
|